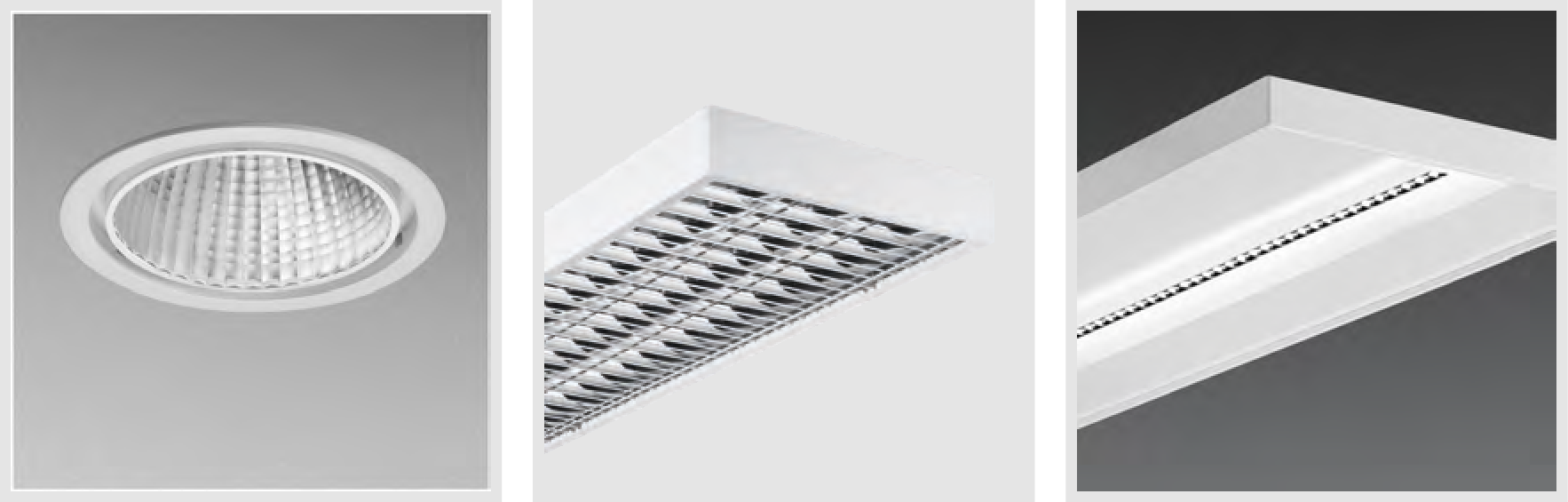
Light distribution by reflection
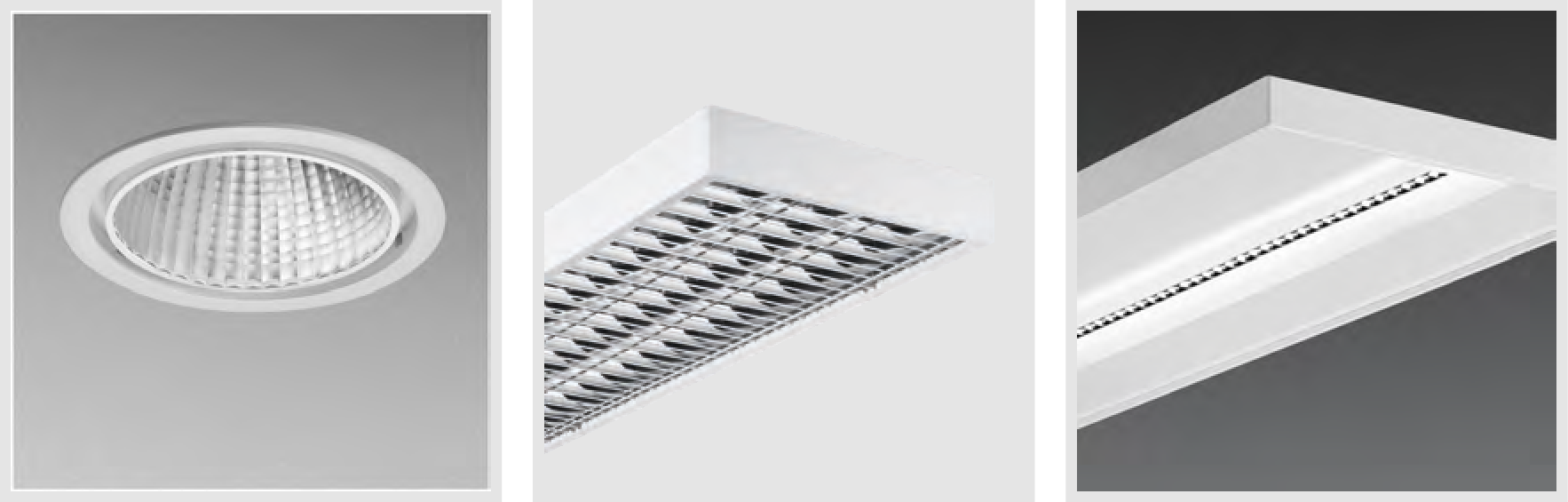
Reflective materials are characterised by their reflectance on the one hand and by their distribution characteristics on the other hand. Aluminium is generally used as a base material for reflectors. By incorporating the reflector into the electrical earthing it is rendered electrostatically neutral and thus insensitive to dust deposits. Plastics are only used as a base in isolated cases due to their electrostatic attraction of dust.
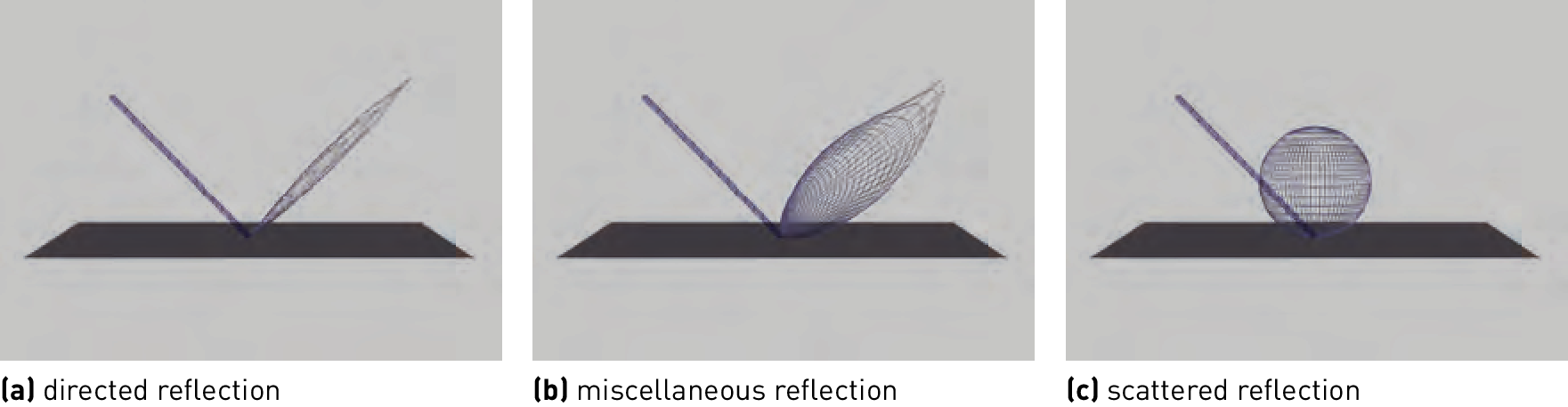
Figure 3.174: Types of reflection
Specular reflection (see figure a) in luminaire technology occurs e.g. on specular reflectors and specular louvres. Exact mirror shapes developed today using computer simulations facilitate the required luminous intensity distribution and luminance limitation of luminaires for the respective lighting task.
Mixed reflection (see figure b), e.g. on semi-specular louvres. In contrast to highly specular materials, this type of surface creates a diffuse portion in the reflected luminous flux. Luminaire surfaces of this type feature a harmonious distribution of brightness and thus are often perceived as pleasant. The more specular component of the reflected luminous flux is used for "defined" shielding conditions.
Scattered reflection (see figure c), e.g. on matt metal louvres, painted louvres or reflectors of corresponding type. Sophisticated painting technologies facilitate reflectance values exceeding 90% and thus range in the dimension of high-quality reflective metallic materials.
Different surface finishes lead to pronounced variations in photometric quality characteristics.
Reflectors painted "Traffic white" (RAL 9016) feature particularly homogeneous reflective properties regarding visible light wavelengths. The light source's light colour and colour rendering index are preserved when reflected. Other white colour tones can cause significant losses in light quality, as is the case with yellowing in paints with inadequate long-term stability.

Figure 3.175: Half-lambda technology
For directed and mixed reflection, there are also several surface finishing processes available today. There is a distinction between
anodised aluminium,
aluminium with reflectivity-enhancing coating, and
aluminium reflectors with silver coated for enhanced reflectivity.
Anodised aluminium is coated with a protective anodised layer directly upon exiting the roller. Anodised reflector materials facilitate sound price-performance ratios and provide proven surface protection for many applications when it comes to aluminium louvres and reflectors, making them age-resistant and uncomplicated in terms of maintenance. The reflectance of anodised aluminium, however, is 85% maximum. Particularly in cases of heavy light direction via multiple reflection, there are significant optical losses.
Aluminium with reflectivity-enhancing coating is the result of improved manufacturing technology. The necessary mechanical stability for its exact shape is provided by an aluminium base (substrate) with comparatively low reflectance. This base is then high-vacuum vapour-coated with one layer of high-purity, high-reflectance aluminium. Subsequently, this layer is coated with a reflectivity-enhancing, highly transparent oxide layer system using a special coating method. At a certain thickness of the transparent layer, which depends on wavelength, angle of incidence and refractive index n, the amplitudes of the reflected light waves add up and thus enhance reflectivity. The path length in the transparent layer must equal (2n+1) · λ/2, with λ being the wavelength of the light (half-lambda technology, figure a).
If layers of varying thickness are applied, several wavelengths are intensified. The overall reflectivity of aluminium with reflectivity-enhancing coating amounts to ca. 95% (see figure a).
Silver with reflectivity-enhancing coating consists of the reflective material high-purity silver, which is vapour-coated onto a pre-anodised aluminium base at minimal layer thickness. Compared to high-purity aluminium, high-purity silver provides significantly greater overall reflectance (silver, highly polished, 90% to 92%; high-purity aluminium, highly specular, 80% to 85%). Through a top layer system enhancing reflectivity (figure b) another increase is effected, elevating the overall reflective value to a value of up to 98% while providing indispensable surface protection. This technology can be applied to highly specular surfaces with a diffuse reflected component of less than 3% as well as semi-specular surfaces (see figure b).
Particular manufacturing methods where the silver layer as well as reflectivity-enhancing layers are applied in a high vacuum facilitate the use of silver, which is sensitive to oxidation, even in environmental conditions found in typical indoor luminaire operation by providing ideal surface protection. In a time-lapse experiment, reflective capacity after 10 years of exposure to aggressive environmental conditions (such as the acidifiers SO2 and NO2 as well as their products with water (acids)) was studied. A visual assessment before and after this exposure showed no differences in the reflective material. Overall reflectance proved similarly stable.
The high measure of overall and directed reflectivity is the basis for a nearly loss-free emission of the light sources’ luminous flux even in small constructions. In luminaire manufacturing, this material is therefore excellently suited for achieving high efficiencies in connection with LED light sources.